УДК 621.311.2
Власов Сергей Александрович,
магистрант,
ОГУ им. И.С. Тургенева,
Россия, г. Орёл
Ющенко Дмитрий Михайлович,
магистрант,
ОГУ им. И.С. Тургенева,
Россия, г. Орёл
Фролов Михаил Викторович,
магистрант,
ОГУ им. И.С. Тургенева,
Россия, г. Орёл
Марков Владимир Владимирович,
кандидат технических наук, доцент,
ОГУ им. И.С. Тургенева,
Россия, г. Орёл
РАЗРАБОТКА ПРОЕКТА МЕТОДИЧЕСКОГО И ТЕХНИЧЕСКОГО ОБЕСПЕЧЕНИЯ КАЧЕСТВА ХОЛОДИЛЬНЫХ ВИТРИН
Аннотация: Предметом исследования является процесс обеспечения качества холодильных витрин. Статья раскрывает некоторые недостатки принятой на конкретном производстве методики контроля качества продукции, в частности, герметичности хладоагрегатов холодильных витрин. Представлены рекомендации по повышению точности обнаружения утечек.
Ключевые слова: холодильная витрина; качество; методическое обеспечение; техническое обеспечение; контроль герметичности
Vlasov Sergey Alexandrovich,
master student,
OSU them. I.S. Turgenev,
Russia, Oryol
Yushchenko Dimitry Mikhailovich,
master student,
OSU them. I.S. Turgenev,
Russia, Oryol
Frolov Mikhail Vasilievich,
master student,
OSU them. I.S. Turgenev,
Russia, Oryol
Markov Vladimir Vladimirovich,
candidate of technical sciences, associate professor,
OSU them. I.S. Turgenev,
Russia, Oryol
DEVELOPMENT OF THE PROJECT OF METHODOLOGICAL AND TECHNICAL SUPPORT OF THE QUALITY OF REFRIGERATED DISPLAY CASES
Abstract: The subject of the research is the process of quality assurance of refrigerated display cases. The article reveals some of the shortcomings of the product quality control methodology adopted in a specific production, in particular, the tightness of refrigeration units of refrigerated display cases. Recommendations for improving the accuracy of leak detection are provided.
Key words: refrigeration showcase; quality; methodological support; technical support; tightness control
Введение. Выполнение данного проекта основано на длительном, порядка 15 лет, опыте непосредственного участия автора в производственных процессах предприятия по изготовлению холодильных витрин – ООО «Фригогласс Евразия». Это предприятие финансово сильное, выпускаемая им продукция (холодильные витрины) имеет стабильный спрос и широкий модельный ряд. На предприятии большое внимание уделяется повышению эффективности производства, оптимизации сборочных линий, увеличению количества произведённых холодильников за единицу рабочего времени, но при этом, к сожалению, вопросы качества, на данном этапе развития завода, отодвинуты на второй план. Все современные этапы производственного контроля соблюдены, все рекомендации сертификационных органов на соответствие требованиям международного стандарта ИСО 9001 выполняются, однако «усердия» в деле повышения качества готовых изделий не наблюдается. Поэтому проблема повышения эффективности процессов контроля параметров холодильных витрин является актуальной для предприятия.
Содержание проекта. В рамках выполнения проекта в направлении методического и технического обеспечения процесса контроля герметичности хладоагрегата холодильной витрины были проведены наблюдения и выявлен ряд недоработок в методах контроля герметичности холодильной системы осуществляемых нашим предприятием на настоящий момент.
Ввиду простоты рабочего процесса, современный холодильник можно признать достаточно надёжной машиной. Единственным «слабым местом» охлаждающих устройств является целостность внутренней полости агрегата, состоящей из трубок различного диаметра и различных материалов. При этом расчётное количество хладагента (фреона), заправленного изначально в хладоагрегат, должно сохраняться в течение всего срока службы устройства.
Условия современного рынка ставят любой вопрос на весы, с обратной стороны которых – цена. Соответственно можно сделать «исключительно» но дорого, можно дёшево, но «впустую», поэтому важно определиться и с нашими целями, а минимально необходимые цели в области качеств и производства диктуют государственные нормативные документы.
Согласно требованиям ГОСТ 23833-95, «Холодильная система должна быть герметичной» (п. 5.1.13), а «средняя наработка на отказ должна быть не менее: 14000ч – для шкафов среднетемпературных» (п. 5.1.32) [1].
Соответственно, на примере холодильника с расчётной необходимой дозой заправки хладогента, равной 100 г., минимальная рабочая доза составляет:
100 – 9 = 91 г.
То есть в течении 1,5 лет (14000 часов), в соответствии с нормативными документами, предприятие имеет право выпустить с заводского конвейера витрину с утечкой хладогента не более 5,6 г./год. Именно на контроль этого показателя будут настроены течеискатели предприятия. И в этом вопросе предприятие выдерживает критику.
Практика показывает, что завод обеспечен приборами высокой точности, позволяющими выявлять утечки хладогента подобного уровня значений. Производство оборудовано течеискателями масс-спектрометрического типа (рисунок 1) [2].
Эти приборы универсальные и точные, но в какой атмосфере приходится работать этим инструментам контроля?
Первая точка контроля герметичности – станция гелий-теста. Это машина полуавтоматическая, действия оператора сводятся к подключению шлангов аппарата к концевым трубкам агрегата холодильника, заправочной и технологической, посредством быстросъёмных муфт, запуск цикла проверки кнопкой «Старт». Аппарат, по программе, производит опрессовку хладоагрегата азотом, с контролем давления в течение нескольких секунд.
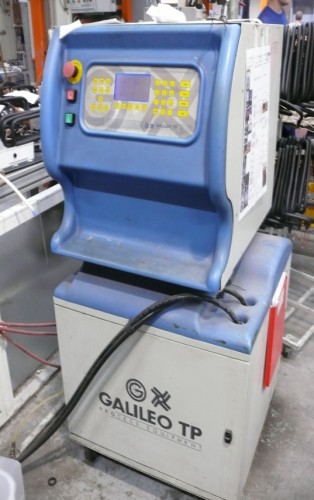
Рисунок 1 – Течеискатель масс-спектрометрического типа
Ремонтная служба следит за состоянием быстросъёмных муфт и своевременно меняет уплотнения, поэтому ложные нарушения герметичности практически исключены. Затем происходит удаление азота из системы и закачка объёма гелием. Вот здесь и включается в работу течеискатель, и проявляются первые недостатки. Отсутствие полноценной потоковой вентиляции, постоянные шумы ввиду работающей в непосредственной близости гелиевой станции, и субъективные ошибки контролёров, связанные с «человеческим фактором».
В целом полноценного и точного контроля на данном этапе добиться, в условиях предприятия сложно, несмотря на настройки данного течеискателя, который настроен на определение гелия (тестовый газ) с чувствительностью до 5 х 10-6 миллибар х л/сек.
Ложные срабатывания практически сводят процедуру контроля до бесполезных манипуляций, сбросы сигнала и повторные обследования того или иного шва на трубках вынуждают оператора не обращать внимания на сигнализацию. А ещё большим недостатком работы данной точки контроля, нужно считать возложенные на работника, в дополнение к управлению течеискателем, сборочные операции, например прокладку кабеля. Это приводит к проведению контроля утечек по остаточному принципу. Собрал элемент, а в оставшееся время обследовал сенсором сигнализатора пару швов (рисунок 2).

Рисунок 2 – Внешний вид корпуса и цифрового табло течеискателя
Далее по конвейеру следует линия вакуумирования агрегатов перед заправкой хладагентом. Отсасывание воздуха производится вакуум-помпами с автоматической сигнализацией недостаточной глубины вакуумирования – вакуум-манометрический тест. При этом глубина разряжения установлена на значение 0,08 х 10-2 миллибар с продолжительностью от 2 до 8 мин.
В данной процедуре единственный критический момент – своевременное обнаружение и выбраковка соединительных муфт с изношенными резиновыми уплотнениями. При внимательной работе заводской ремонтно-сервисной службы, этот момент не проблема, и на качество продукции в конечном итоге действия не оказывает [3, 4].
Процесс заправки хладоагрегата холодильной витрины рабочей дозой хладагента производится заправочной станцией (рисунок 3). В нашем случае – это универсальный прибор, который работает со всеми современными хладагентами, включая горючие. Сразу после подключения головки, машина в автоматическом режиме проверяет глубину вакуума системы, и при нарушении установленного значения «объявляет тревогу». Холодильник с полностью заправленным агрегатом и практически готовый к работе, поступает на линию проведения функционального теста, а в её начале, практически сразу после заправочной станции, установлен второй течеискатель, настроенный на хладагент. Здесь, на проведение полноценных испытаний герметичности рабочего агрегата, так же оказывает влияние отсутствие обдува и эффект срабатывания сенсора на возможные диффузионные шумы молекул хладагента. Вся задняя часть холодильника во время отключения быстросъёмных соединительных муфт, подвержена бомбардировке молекулами хладагента, во время сброса давления из под освобождённого уплотнения. И уже на данном этапе без принудительной направленной вентиляции поверхностей не обойтись, поэтому её отсутствие является существенным недостатком процесса заправки хладоагрегата.
Поэтому происходят ложные срабатывания и сбросы сигнала, повторное сканирование, что приводит к потере рабочего времени и производительности труда. А это периодически приводит к тому, что на участке приёмочного контроля технические контролёры пропускают холодильники со скрытой утечкой фреона, которые затем попадают к потребителям.
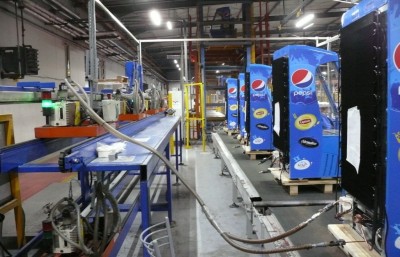
Рисунок 3 – Процесс заправки хладоагрегата витрины хладогентом
Также несколько слов хочется уделить ещё и такому немаловажному аспекту контроля герметичности, как обследование того или иного элемента трубопровода холодильной системы течеискателем, в тот или иной временной отрезок работы компрессора. Например, трубки высокого давления: нагнетающая, капиллярная, конденсатор логичнее проверять в момент включенного компрессора, когда давление в указанных магистралях – повышенное. А вот всасывающую линию (обратная трубка), испаритель, сам компрессор, правильнее сканировать в процессе отключенного, неработающего мотора, когда указанные элементы находятся под повышенным давлением изначально заправленного в агрегат фреона. Но мало того, что эти этапы работающего холодильника разнесены по времени, так ещё и противоположны по месту размещения на витрине. То есть, испаритель, всасывающая трубка (большая её часть), часть капиллярной трубки, размещены внутри рабочего объема охлаждающего шкафа, и имеют доступ только через дверь с фронтальной части, а компрессор, конденсатор, нагнетающая линия – это, как правило, задняя часть или агрегатный отсек. И соответственно, чтобы избежать перемещения контролёра вокруг холодильника с течеискателем в виде тяжёлого стационарного прибора, необходимо как минимум, располагать двумя, а в идеальном случае несколькими инструментами контроля.
Обсуждение результатов. Всё описанное выше указывает на то, что мало приобрести современные точные чувствительные приборы, необходимо также иметь соответствующую инфраструктуру предприятия и необходимые окружающие, зачастую специальные условия работы средства контроля. В конкретном случае наличие двух или более участков с принудительным обдувом зон и вентиляцией в них рабочей атмосферы, на порядок снизило бы вероятность выпуска заводом продукции ненадлежащего качества.
Для повышения производительности процесса контроля качества холодильных витрин предлагается разработать комплекс методического и технического обеспечения процесса контроля. Техническое обеспечение процесса контроля включает в себя комплект оборудования: оптическое оборудование для экспресс-контроля качества паяных швов хладоагрегата холодильной витрины, работающее по принципу сравнения изображения реального паяного шва с эталонным изображением; ультразвуковое оборудования для неразрушающего контроля паяного шва хладоагрегата холодильной витрины, которая по результатам оптического контроля была изолирована для более достоверного контроля.
Методическое обеспечение процесса контроля включает в себя комплект методик: методику сравнения фотографического изображения реального паяного шва с изображением эталонного шва; методику сканирования ультразвукового зонда по поверхности трубок хладоагрегата; методику расчёта координат залегания и размеров дефектов паяного шва; методику оценки рисков снижения качества холодильных витрин, в соответствии с которой будут разрабатываться действия персонала по предупреждению дефектов.
Список литературы:
1 ГОСТ 23833-95. Оборудование холодильное торговое. Общие технические условия. – Мн.: Издательство стандартов, 1995. – 135 с.
2 Мак-Гоннейгль, У. Испытания без разрушения / У. Мак-Гонннейгль. М.: Машиностроение, 1965. – 352 с.
3 Сакун, И.А. Холодильные машины / И.А. Сакун. – М.: Машиностроение, 2011. – 506 с.
4 Жаккар, П. Пособие для холодильшиков-практиков / П. Жаккар, С. Сандр; Пер. с англ. М.П. Кожевина. – М.: Мир, 1997. – 680 с.
|